Consumers looking for the “best” AR15 rifle are often left with option overload. If you want to find the best, you end up researching for hours and still only find subjective data… or you might end up clicking through “Top 5 AR15” type articles, but most of those articles are nothing but click-bait. Worthless. Insulting. So who *really* makes the “best” AR15? Who makes the best barrel? Who makes the best free float rail? Who makes the best AR15 stock system?
What is best in life? Accuracy? Reliability? All of the above?
Welcome, my friend… to the Data Driven AR15 Project.

“What is best in life?”
Jump to Chapters:
So who does makes the best AR15? The truth is, no one. There is not one manufacturer who alone holds that golden key. The AR15 continues to evolve; countless manufacturers are striving to deliver components that improve on the original design. In the last ten years, the industry has produced components that truly break new ground, and some that simply fall flat. Which of these products drive the AR15 into the future and improve on its reliability, accuracy, and handling? Which of these products do nothing more than put lipstick on a pig?
How do separate the wheat from the chaff? Data. Studies. Are you ready?
Let’s kick this pig.
THE DATA:
This article procures data from a variety of sources. For some studies, we must ask the manufacturer to release the data, and for some we must rely on published military testing. Yet for others, we must rely on consumers who take the time and effort to quantify the data. Not all data will be collected in a laboratory setting, but we are going to use our best efforts to source quality studies and references. This article will present arguments for the “best” individual components and present data to back it up. Not every component will fit everyone’s idea of what is best in a rifle, and not all data will fit every individuals taste for scientific credibility, so I look forward to your responses below.
Stock and Buffer System:
It would be safest to assume that a collapsible stock is the de-facto modern standard for an AR15 due to its adjust-ability to shooter size, the ability to modify length to suit armor, and its ability to shorten the weapon for storage. Fixed stocks have proven to be problematic for each rifleman is unique and there is no “one size fits all” stock. When the Marines adjusted the length of pull through the M16A1 PIP program, the Army was none too pleased:
The M16A2 stock Is too long for Army use. The decision to lengthen the stock was made after all portability tests (entering and exiting aircraft/ vehicles/buildings, etc.) had been completed and without consideration for body aimor, field jacket with liner, load bearing equipment, etc. This change results in the M16 trigger to butt plate length (the test report states 14 inches) being approximately one inch longer than the Springfield, Ml, or M14. The Army problem was that the existing (A1) stock was already too long for many soldiers (mostly females). *1 ANALYSIS OF M16A2 RIFLE CHARACTERISTICS AND RECOMMENDED IMPROVEMENTS
Yet there is validity in maintaining that fixed stocks and their buffer system are the de-facto standard for high reliability in a Ar15/ M16. Industry approaches to enhancing reliability and improving the recoil impulse of the AR15 have centered around the development of heavier buffers and/or unique buffer and spring configurations. There exists a variety of alternative buffer systems which depart from Stoner’s design and instead opt for complex configurations with proprietary components.
In my opinion, it is in the rifleman’s best interest to maintain some backwards compatibility with traditional components when selecting products. However, it is also in the rifleman’s best interest to improve upon the AR15 system by adapting incremental changes and improvements which are driven by data. The H6 buffer has been gaining in popularity as it replicates the weight of the M16 rifle buffer while fitting into the collapsible stock form factor. At some point, the military began to test collapsing stocks as a possible future upgrade to the M16A4. Included in the test were the traditional A2 style stock, a H6 equipped carbine telestock, and Vltor’s A5 system.
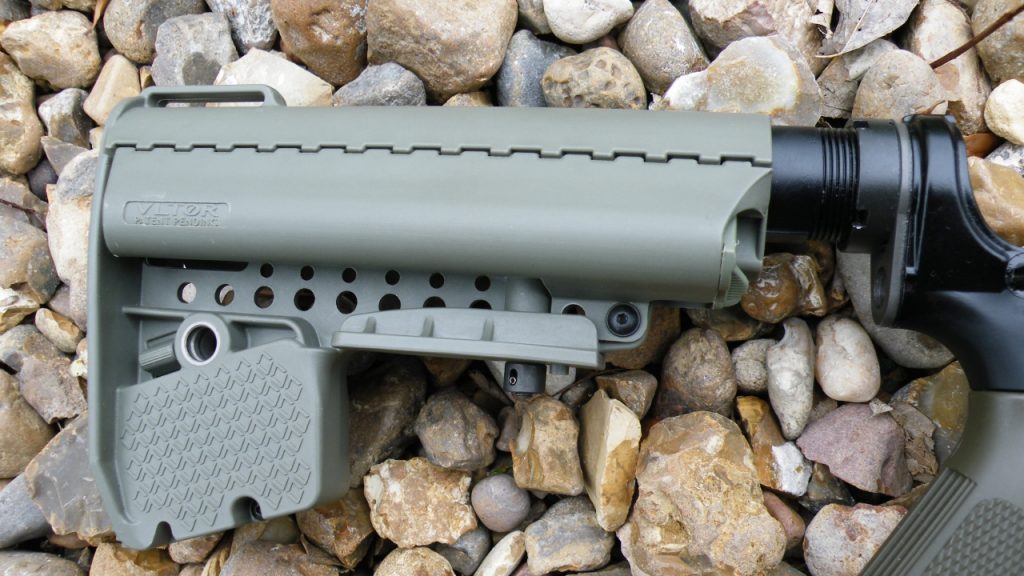
The Vltor A5 looks unassuming, until you see the data:
The Vltor A5 telescoping stock appears to have outperformed the M16A2 fixed stock and buffer assembly and indeed bested the H6 equipped carbine in performance. While it is somewhat hard to read, the following link details the results of the H6 vs A5 vs M16A4 buffer assembly (which is identical to the A2):
In almost 60,00 rounds of testing, the A5 system slightly outperformed the H6 buffer and the standard A2 buffer system. This slight gain on reliability over the standard stock system along with the ability to collapse for the perfect length of pull make the A5 a must have piece of kit. I must also mention that it uses a standard rifle length buffer spring and can still be fitted with other Mil-Spec diameter stock assembly’s to tailor it to a rifleman’s preference. Hat’s off to VLTOR for developing and delivering a stock and buffer assembly that supersedes all other designs that we know of at this point.
Receivers and Rails:
Many manufacturers produce enhanced or reinforced upper receivers that promise increased thickness and strength. There are also upper receivers that are coated in proprietary and expensive coatings that deviate from the standard mil-spec receiver, but do are these products worth the cost?
The upper receiver is actually a low wear component. As Henderson Defense (a large gun rental range in Las Vegas) notes on Ar15.com, the upper receiver practically never wears out. Excess of 100k rounds are reported in receivers that have experienced high volume sessions through their rental range:
“Some of our M4’s have well over 200,000 rounds down range. Barrels have been replaced, gas tubes have been replaced, BCG’s have been replaced but what sets it apart from the AK47’s is that upper and lower receivers continue to function. AK’s get to about the 100,000+ round count and rails on the receiver will start to crack. It’s an easy fix with tig welding but they crack. We have yet to lose an upper or lower receiver from cracking.” Henderson Defense, AR15.com
This is an interesting data point. While not a true “study”, Henderson Defense keeps usage logs of their range rental rifles. Noting that upper receivers have yet to wear out means we can work past the coating hype and simply buy a standard forged upper receiver with proper anodizing and a dry film lube as per mil-spec. So long as it is made properly, the “standard” forged receivers can be considered a long wear item suitable for a hard use rifle. Coatings such as Nib-X and other “wonder coatings” can be bypassed as simply unnecessary from a long term reliability perspective.
So if fancy coatings and other reinforcements are unnecessary, then what, if any, products improve on the design of the standard upper receiver?
There have been numerous designs over the years, ranging from the LMT monolithic system (which remains patented), to derivatives of this design such as the Aero Precision COP, M4E1/M5 platforms, Mega Machine Megalithic AR15 upper receiver, the Vltor VIS system, as well as many others.
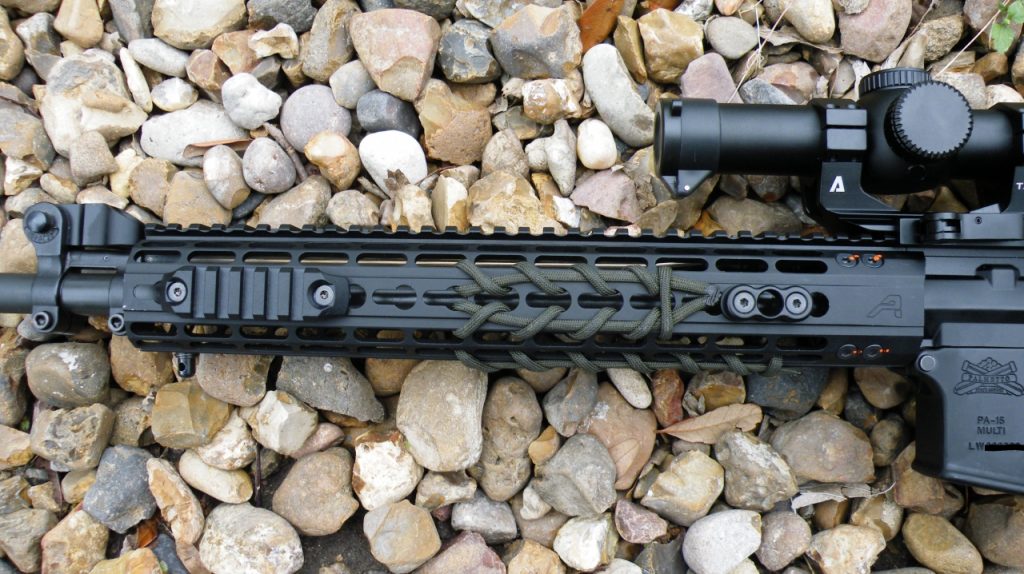
The Author’s Aero Precision M4E1 is an integrated handguard and receiver.
It is my belief that integrating the rail and upper receiver and removing legacy components such as the delta ring, standard barrel nut, weld spring, etc. are a means to simplify manufacturing and reduce the overall complexity of the platform, but that is simply my opinion. Do the monolithic, polylithic, and other modular upper receivers that move past the traditional design improve on performance in any way?
Insofar, a quality made upper receiver fitting within the standard mil-spec for anodizing and finishing will last a lifetime of use, be it a standard or integrated hand-guard unit. Without reference data we are unable to provide much discussion as to the mechanical merits of the integrated upper receiver and hand-guard combinations other than reducing parts count which is notable, but not necessary. Of all the mentioned upper receivers, I have procured a limited data set regarding the Aero Precision M4E1. Please keep reading below in the Rails Section.
What is the best rail system? That’s question doesn’t have a definite answer, but we can related question: which is the better rail attachment method, KeyMod or M-Lok? This topic has been rehashed over and over upon since the introduction of M-Lok into the marketplace. Numerous manufacturers have jumped into the modular rail game due to ease of manufacture, cheaper cost, and the ability to sell more attachment accessories. Both competing systems offer a modular means of accessory attachment, but does any data point to one or the other as the stronger system?
Yes.
In a recently published study by CRANE, the M-Lok accessory atachment system was shown to wipe the floor with Keymod in several criteria: M-Lok had less point of impact shifting when re-attaching accessories, it had less failures during the drop test, and M-Lok had almost three times the strength of KeyMod system when bearing load.
The data shows M-Lok to be far stronger than KeyMod.
The Crane summary paints a very clear picture as well and touches on the high points succinctly:
The data doesn’t lie. KeyMod fails to preform to the level of M-Lok during the Crane testing. This type of information is invaluable and is certainly applicable to the data driven AR15. I load my bipod, and currently use KeyMod. How long till I pop out my bipod over years of stress to the system? I don’t want to find out. I will be moving to M-Lok as part of my quest to build the ultimate Data Driven AR15. Also of note, the rails tested included Aero Precision’s M4E1 system. The Aero Precision A3/A6 sample proved to be the strongest rail system when force was applied to either Keymod or M-Lok. Other rails tested include a Seekin’s Precision and Midwest Industries rail. While these three rails represent a fraction of the available rail systems, it is still an excellent showcase of the M4E1’s strength.

The M4E1 upper receiver and rail system proved to be the toughest receiver (of 3) tested in the crane Key-Mod vs MLOK study.
The Bolt:
Ah. What a mythical (or is mystical?) area of the AR15 to discuss! The two most common arguments are that enhanced brand x,y,or z bolt is the best, or that the standard, mil-spec bolt is the best if it is made to the TDP. Change the oil every 3000 miles and live with it is often the solution pushed to those wanting to ensure their bolt doesn’t fail at the wrong time. The standard, mil-spec bolt works and so long as bolt replacement is done at x rounds, there is no need for a design change. Right?
Well, I would disagree with that. Lab testing analysis of the M16 bolt carrier revealed what has been long known… the locking lugs immediately adjacent to the extractor face more stress than the other lugs on the bolt, and subsequently are the first to break:
In particular, higher stress concentrations were present in the locking lugs which were immediately adjacent to the round extractor. These two specific locking lugs experienced stresses on the magnitude of approximately 1070 MPa as shown in Fig. 4(b). All of the five fractured bolts analyzed at the Army installation had fractured at these specific locking lugs. … In addition, these extremely high stress concentrations contributed to the crack initiation which is evidenced by the picture of a crack growing from the locking lug next to the round extractor, as shown in Fig. 6. – Failure Analysis of the M16 Rifle Bolt
The standard AR15 bolt could stand some improvement. When pushed harder in shorter or suppressed weapons, the bolt’s life is shortened and the potential for lug failure is exacerbated. A variety of manufacturers have attempted to “fix” or enhance the bolt group while staying inside the design parameters of the standard AR15 barrel extension. I inquired with several companies which produce enhanced bolts, but failed to receive any data or, in some cases, a response. Matthew at JP Enterprises did respond to my inquiry, but he noted that the internal testing data was considered a guarded IP. I understand his position, but until we can find a way to get some hard data released, we may never know how the bolts truly perform or in what way they are “enhanced” over standard bolts… however occasionally very interesting tidbits of information sprinkle out for the taking. Take, for example, Bill Alexander’s discussion of the LMT Enhanced Bolt:
The bolt itself is of particular interest. The function of the dual spring extractor is frequently misinterpreted as an attempt to add spring force to the extractor claw. Rather it reduces the fatigue that the extractor spring(s) undergo by allowing the use of longer springs with lower K values; the % relative compression during the movement of the extractor is reduced. … The traditional Carpenter 158 is abandoned, being replaced by a significantly tougher grade from a different manufacturer. The lugs themselves are generously radiused between lugs and at the rear the diameter is actually reduced to allow a larger transition radius to be machined. The incorrectly identified sand cuts on the lugs are stress relief cuts. These allow any individual lug to elastically deform and give a smoother load over the contact patch. While this type of feature is very difficult to calculate and even more difficult to implement it helps to place the lug in a true shear load rather than amplify the bending moment. As noted the lug opposite the extractor is relieved. This feature prevents the unequal transfer of load to the two opposite lugs but I would argue that the stress relief groove already in place largely accomplishes this purpose. This is a academic quibble so I will bow to LMT in this respect. There is one additional feature that can be found in the bolt, but I am not at liberty to disclose the detail. – Bill Alexander Discussing the LMT Enhanced bolt at M4 Carbine.net
The above is excellent information, but without data we cannot claim LMT’s product as a data driven option. Does it work better than a standard bolt? There is no data we can access. So how do we separate the pixie dust from real stuff? I do have one study here to bring us back to reality: the Army has pursued testing and analysis of new techniques to work harden the bolt. The study has been declassified and released to only the saaviest of internet bloggers such as myself. The US ARMY RDECOM (Research, Development, and Engineering Command) has tested a method of cold work hardening a bolt that shows a substantial increase in bolt life. Here is a short excerpt of the power point findings:
• Live Fire Testing – Single Weapon Test (M855) • LPB Bolt ~ 26,000 rds fired before failure
• Standard Bolt ~ 13,000 rds fired before failure
– “Low Plasticity Burnishing for Fatigue Life Extension of the M4A1 Carbine Bolt”
Having this data made available to the public from a well respected organization means we can move past the “enhanced” hype and direct our attention to processes improvements that increase bolt longevity without “pixie dust” claims by manufacturers. Lambda Technologies assisted with the testing and is a private company. Upon inquiry, they have stated that several civilian companies have contacted them but a NDA will shield those relationships for now. Should a manufacturer want to incorporate Lambda’s roller burnishing process into their bolt, it would give our community a data driven process that would push the reliability and durability of the AR15 forward by doubling the life of an otherwise standard Carpenter 158 bolt.

Data Driven: Low Plasticity Burnishing and the M4/M16 bolt
I would be first in line for a DATA DRIVEN product such as a burnished bolt. It is such a simple process that has proven to work in the real world without adding fancy coatings, it works without insane Cthulian lug geometry, and bypasses the expense of non-standard bolt steels. Low plasticity burnishing of the bolt is data driven, and the process deserves a place in the modern AR15.
The Best Barrels:
Another heated point of discussion are the merits of barrel x vs barrel y. We have multiple forms of rifling, multiple barrel profiles, and a variety of lengths. Picking the “best” is often a exercise in opinion versus science and data. True, top competitors often use a small handful of brands… as competitors seeking an edge often gravitate towards proven products, but data is not always available to back up their choices.
When discussing the “best” barrel, a number of factors will come into play. The perfect barrel would shoot with match accuracy, weigh nothing, and would never wear out. Since we cannot achieve such a wonder material at this point in time, we are left with a mixed bag of products, profiles, treatments, and linings that consumers must choose from to mix barrel life, accuracy, and weight into a package that they deem suitable for their purposes.
One of the unique products I have stumbled upon and have used personally is the Criterion “Hybrid Contour Match Chrome Lined barrel”. The claims of the product being “match grade”, yet chrome lined, piqued my interest. The Hybrid Contour is a tapered profile so it blends a high strength to weight ratio. Looking towards our mythical “perfect barrel” with infinite barrel life, zero weight, and pin-point accuracy… it would seem that the Criterion’s feature package makes fewer trade offs compared to other market offerings. So do we have hard data?
The team over at Science of the Gun has offered the community a comparison test with hard data. The test pits three light-weight profile barrels against one another in a shootout with various brands of ammunition and then averages the data.
The results show great promise for the Criterion Hybrid barrel. The overall average 10 shot group from the Criterion Hybrid Profile barrel was 1.8 MOA with Larue running a close second at 2.04 MOA. This is an average over 10 different brands of match ammo. What’s interesting is that Criterion’s submission is chrome lined.
By delivering a chrome lined barrel that is truly *match accurate* in a high strength-to-weight tapered profile, they have nudged the rifle barrel a few inches closer to the “perfect” barrel. They outperformed, however slightly, a tapered profile barrel from Larue Tactical and Ballistic Advantage. Again the results are often within a few tenths of minutes depending on brands of ammo, but the averages don’t lie. If Criterion was able to bests both competitors in accuracy, however slightly, and did so with a chrome lined bore and chamber… this is a substantial advancement in barrel longevity and accuracy.
…but is this the pinnacle of barrel technology? Criterion’s product is more like a refinement of already established technology. There are several active companies that offer barrels which attempt to re-imagine barrel technology and push some bold claims: stiffer yet lighter than steel, products that shed heat faster than steel, minimal point of impact shift over a large range of temperatures, etc. Several companies offer carbon fiber barrels, and one even offers a extreme “jacketed” barrel, sleeve, and substrate combo that is an even more radical departure from even carbon fiber barrels. So where is the data? Do these sci-fi barrels perform? I found the data I needed from another well-respected source: Bryan Litz “Modern Advancements in Long Range Shooting Vol. 2” has the testing data I seek.
In Litz’s book, co-author Cal Zant was able to pit many traditional barrel designs against high tech products in a well documented performance shoot out. The following companies were represented in the test: Proof Research, Christiansen Arms, Teludyne Tech, as well as several brands of traditional steel barrels in heavy palma profiles (x2) and traditional barrels in lightweight and fluted forms. The barrels were attached to bolt action rifles, chambered in 6.5 Creedmore, and evaluated for stiffness, accuracy, and point of impact shift as the barrel heats. The results were surprising.
Without just spilling *all* the beans on the author’s hard work, I will offer a quick, though incomplete, glance at his data:
- The Teludyne Systems “Straight Jacket” was the most accurate cold barrel and it appeared to shed heat the fastest.
- The Christiansen Arms Carbon Fiber Wrapped barrel had the second best result for minimum point of impact shift as it heat up, shifting only .35 MOA when warmed. It was also the lightest barrel tested.
- The Heavy Palma barrel, was both the heaviest barrel and experienced the least point of impact shift as it heated, besting all other products.
- The fluted and pencil profile barrels were the least accurate and experienced the largest point of impact shift in the testing.
The data presented is awesome, and I highly suggest you purchase a copy of Bryan Litz book to support his ongoing ballistic research and testing. I personally found the light-weight carbon fiber barrel from Christensen Arms to be of particular interest for the AR15 shooter. Do these barrels maintain the same high level of performance when made for the AR15 platform?
I asked Kort Nielson of Christensen Arms if they had any internal testing data regarding the performance of the AR15 series barrels. Does the performance of their AR15 line mimic the awesome characteristics found in Cal Zant’s bolt action test? His response:
The operating system of AR15 platform rifles creates interesting challenges to overcome. By selecting different materials and engineering different barrel designs around minimizing the challenging characteristics of AR’s we have achieved promising results that show similar performance trends.
So take it for what its worth. A purview of the barrel tech has given us a few promising technologies that can drive the AR15 into the future. Christensen Arm’s carbon fiber barrel looks like a exciting test candidate based on the results in “Modern Advancements”. The blend of lightweight carbon fiber, match grade accuracy, and minimal point of shift are intriguing points for a semi-automatic patrol rifle.
Enter Teludyne Tech:
Teludyne Contacted me to evaluate the Straight Jacket system mentioned above. With the right loads, the Straight Jacket groups like a bolt action rifle.
My initial testing of Teludyne Tech reveals some POI shift with heat, but the group size remains the same regardless if the magazine is dumped or if the barrel is slowly heated up. The ability to maintain rifle precision shows us that Teludyne has something which is dampening the harmonics of the barrel making good loads shoot stacked on top of one another. Furthermore, after independent laboratory testing of a barrel before and after Straight Jacket application, the H.P. White Independent Laboratories revealed the barrel to have less POI shift and a higher degree of precision after Straight Jacket Application. The results of this study can be viewed here. I applaud Teludyne for paying for independent lab testing and it further reinforces their claims as being backed by real world data.
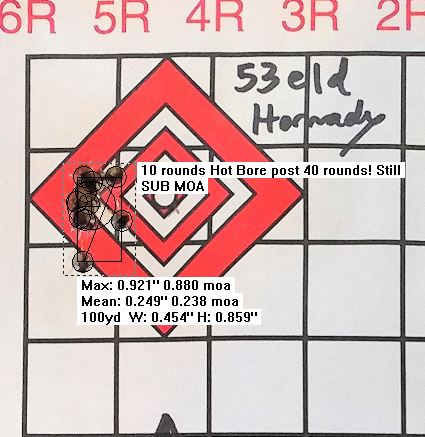
After 40 rounds, rounds 41-50 remain stacked on each other with no obvious sign of group enlargement from heat. This backs up some of the claims from Teludyne Tech.
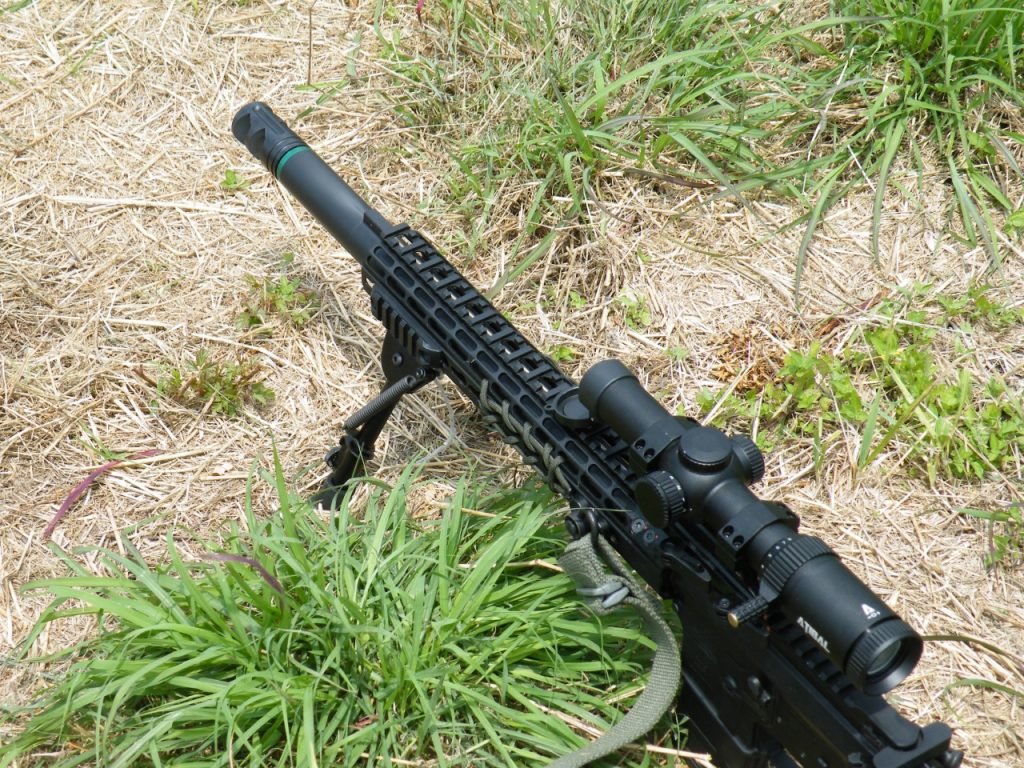
Initial testing reveals that the Teludyne Tech Straight Jacket system does have some POI shift, but the group size remains unaffected by heat.
After an exhaustive review of the Telludyne Tech Straight Jacket system, I can say that it did deliver the most accurate groups I have ever witnessed out of an AR15, but it isn’t without its own quirks. Please review my collection of thoughts on the STJ system below:
The New Rifleman review can be viewed here.
Barrel Stiffness:
I would be remiss to ignore a significant feature that applies to all barrels: Stiffness. As Teludyne points out in their numerous articles, they believe stiffness is a key factor in barrel accuracy. As 55k PSI of pressure surges down the barrel, the metal is prone to resonate in unique ways from load to load. This is known as barrel whip. The barrel is a classic example of a cantilevered beam, and the longer and skinnier it is, the more whip the barrel will have. A short, thick barrel is going to exhibit more consistent accuracy characteristics from load to load than a long skinny barrel. As a long, skinny barrel whips (in a low frequency sine wave) it has the potential to release the bullet on a new point on the X-Y axis with each shot. This reduces precision. A short, stiff barrel will flex less and maintain a higher degree of precision. See this excellent write up by Lilja Barrels HERE. Keep this in mind when you are building as you have to decide which factors are important for the job you want your AR15 to do.
Until I can conduct a formal head to head test of the Christensen Arms carbon fiber barrel, I would recommend that readers look hard at Criterion’s line of hybrid match products because their performance has been proven to be Data Driven.
The Best AR15 Magazines:
The Ar15’s magazine has been called the Achille’s heel of the AR system. The thin aluminum feed lips can be easily bent and damaged, and the military failed to develop the magazine to a level of higher reliability until the early 2000’s. For this I blame the Federal assault weapon ban. Had civilian companies been allowed to develop standard capacity magazines in the 1990’s and let consumers drive competition, the war-fighters in the war on terror may have had high quality magazines prior to the introduction of the ground-breaking Magpul PMAG.
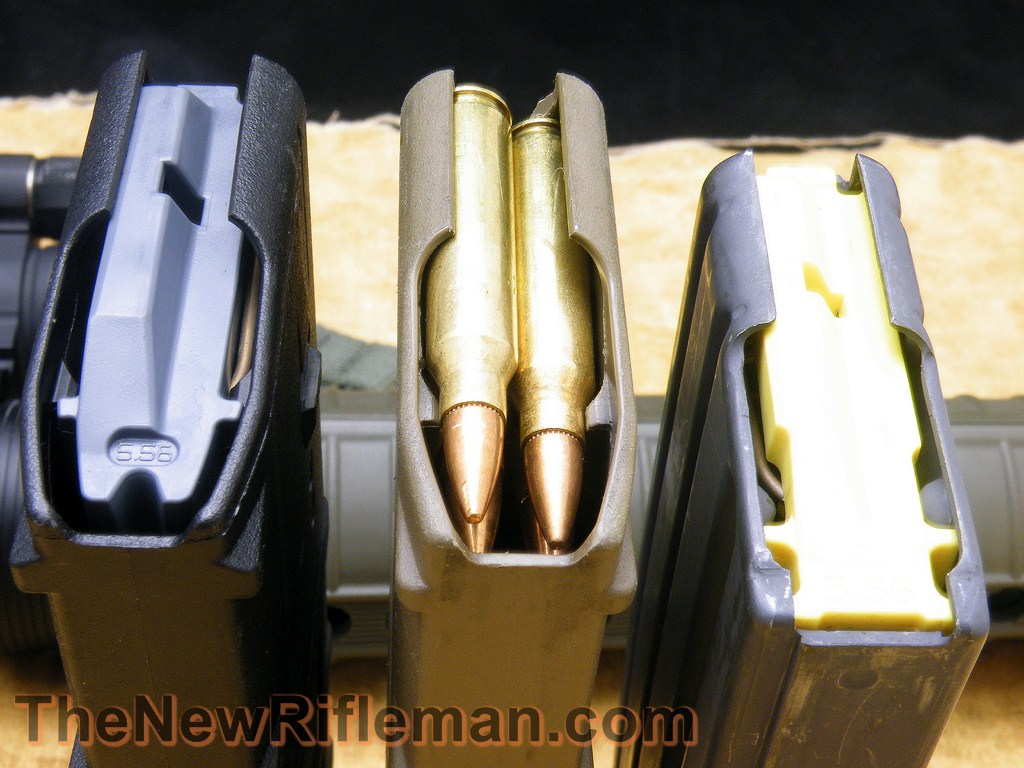
From Left: Gen 3 PMAG, GEN 2 PMAG, USGI with PMAG follower.
Is the popular PMAG the most reliable magazine available for the AR15 / M16 platform? What does the data say? A Marine Corps System Command evaluated several magazines and published the data for our review:
Vendor A is, you guessed it, the Magpul polymer PMAG. It is unknown which generation P-Mag the test evaluated. In both the M4A1 and M16A4 system, the military’s own “Enhance Performance Magazine” failed to usurp the PMAG in reliability between the two ammunition types tested. The Aberdeen Report, which shows an additional slide featuring the M27 weapon system, is available here. The PMAG was truly a game changer upon its introduction, and Magpul’s dedication to innovation and continued upgrades to each generation of magazine solidify their product as the “best of the best“. The above report is just further proof of the product’s superiority.
The Best AR15 Triggers:
Is there a way to scientifically evaluate a trigger? Can we measure creep, grit, take up, and other parameters that can reveal how “clean” a trigger breaks? Of course we can.
Much credit to Jeremy S. for his last few years at “The Truth About Guns“. Jeremy has pushed a scientific approach to gear comparisons that gives us data to work with instead of just hype and subjective review claims. In his article, “The AR-15 Drop-In Trigger Roundup“, Jeremy utilizes the Dvorak TriggerScan to give us a scientific instrument that evaluates trigger pull weight, creep, over-travel, and reset.
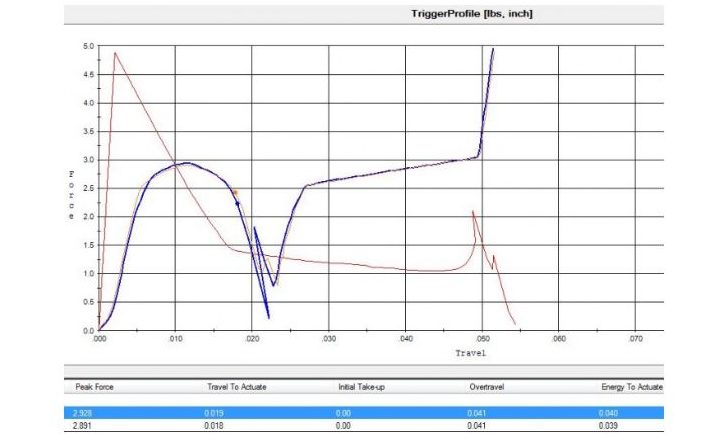
A snippet of some data captured by Jeremy S. and the Dvorak TriggerScan unit. The Elfman trigger group had arguably the tightest set of parameters of all units tested. Subjectively, Jeremy S. noted that this is also his favorite trigger group.
While not comprehensive (the test only evaluates drop in one piece trigger units and absent are “traditional” AR15 triggers such as products from Geiselle) it is a study with both objective and subjective data presented to the reader. Evaluating the data presented reveals the Elftman Tactical Elf-Match / Tactical Trigger to have a tightly defined set of parameters… having both zero measurable take up, a crisp break, no perceptible creep, and a minuscule reset. Comparing the various triggers and graphs in his study reveal that the Elftman unit has a very smooth bell curve from pull to break, where as many other triggers exhibited peaks and valleys of grit or roughness in the pull.
It would appear that Elftman Tactical’s attention to detail has led them to the top of the pack for quality in a drop in trigger unit based on objective measurements coupled with a subjective evaluation. The company has delivered a product which can be objectively measured and the data presented is outstanding and showcases a tight grasp on high quality manufacturing.
The Best AR15 Lubricants:
An AR15 isn’t going to be data driven if we don’t cover another essential component of a functional rifle. Lubrication. A lubes primary job is to reduce friction between moving components. Secondarily, a lubricant can prevent rust and condition metal. With so many competing products, it can be a difficult task to test them. Do we use a lab? Do we go by feel? No. Sometimes enthusiasts can conduct practical experiments and collect pertinent data. Day at the Range did comprehensive test of lubricants and found that Hornady One Shot, WD40 Specialist, and Frog Lube claimed the top spots for both friction reduction and rust prevention.
Many products were tested, and those three products stood out above all the rest in both rust prevention and reduction in friction. Based on the results, I too examined Hornady One-Shot for myself and was blown away by its ability to make my rifles feel smooth during charging and cycling, yet completely dry. Hornady One Shot also performed exceptionally well at rust prevention. Until we have a better sample of data, we will call these results as Data Driven.
Wrapping Up:
So here we are. I hope I have outlined a few points of data that represent components that push the AR15 into the future. I wrote this article in response to the countless “best AR15” articles on the inter-webs that don’t actually substantiate why a rifle or piece of gear is the “best”. Many of these articles aren’t written to advance the cause of the well armed patriot… many of them are written to advance the pocket book and shill products. When I write, I write with high standards. You want a best of the best article, well here it is. Many thanks to the bloggers and AR15 community that strive to write quality “best of” articles such as Jeremy C. over at TTAG. He and countless others advance past the internet trash into a new realm of quality firearm journalism. As for this article… This article is not done. Not by a long shot. This is the *third* update of ongoing draft. Whenever I find a data driven product, design, or change to the AR15 platform, it will be updated here.
We have seen great strides in the AR15/M16 family of weapons, and to continue to drive further into the future, we need to be Data Driven.
If you have any data to share, drop it in the comments below.
Revision 2: Added Key-Mod vs M-Lok data, discussed M4E1 from Aero Precision.
Revision 3: Added PMAG and Aberdeen Report.
Revision 4: Added additional photos of M4E1, closed thoughts on Straight Jacket System
Revision 5: Added Best Lubricants
Sources:
Osborne, Arthur D., Smith. Seward Analysis of M16A2 Rifle Characteristics and Recomended Improvements.
ARI Field Unit at Fort Benning, Georgia. Cited Jan 15, 2017. Retreived from http://www.dtic.mil/dtic/tr/fulltext/u2/a168577.pdf
Author Unkown. DTR – Reliability Comparison M16A4 with H6 Buffer/VLTOR stock. Cited Jan 15, 2017, Retreived from
https://lh3.googleusercontent.com/-hudcJT-wfAo/VHNSFw3-aPI/AAAAAAAAAjg/gnQ7MS3kOUs/w438-h567-no/Vltor.jpg
Litz, Bryan. Modern Advancements in Long Range Shooting Vol II. Applied Ballistics, 2016. 237-269. Print.
Henderson Defense. High round count AR/M4’s (over 100,000 rounds) and how they have handled on our range. [web forum comment] Retreived From http://www.ar15.com/forums/t_3_118/677135_High_round_count_AR_M4_s__over_100_000_rounds__and_how_they_have_handled_on_our_range.html
V.Y. Yu *, J.G. Kohl, R.A. Crapanzano, M.W. Davies, A.G. Elam, M.K. Veach. Failure Analysis of the M16 Rifle Bolt.
Cited Jan 15, 2017. Retreived from http://www.ewp.rpi.edu/hartford/~ernesto/F2014/MPT/MaterialsforStudents/Flavin/Yu2004-FailureAnalysis-M16RifleBolt.pdf
Alexander, Bill. LMT Enhanced Bolt Question. [web forum comment] Retreived from http://www.m4carbine.net/showthread.php?3379-LMT-Enhanced-Bolt-Question/page2
Grego, Thomas C., Foltz, Adam L. Low Plasticity Burnishing for Fatigue Life Extension of
the M4A1 Carbine Bolt. U.S. Army Research, Development and Engineering Command. Cited Jan 15, 2017.
Retrieved from http://www.dtic.mil/ndia/2016armament/18263_Grego.pdf
“Bryan and Nick.” Barrel Overview using Extreme Spread of Targets. Science of the Gun. Cited Jan 15, 2017.
Retrieved from http://www.scienceofthegun.com/?p=236
Jeremy, C. The AR-15 Drop-In Trigger Roundup. The Truth About Guns. Cited Jan 15, 2017. Retreived from
http://www.thetruthaboutguns.com/2016/04/jeremy-s/ar-15-drop-in-trigger-roundup/
Elder, JT., Seidle, Brett. KeyMod vs. M-Lok: Modular Rail System Comparison. Cited May 9th, 2017. Retreived from http://www.thefirearmblog.com/blog/wp-content/uploads/2017/05/Crane-M-LOK-vs-KeyMod.pdf
“DIY_Guy.” Comprehensive Corrosion Test: 46 Products Compared. Cited Aug 2, 2019. Retreived from http://www.dayattherange.com/?page_id=3667
Another excellent write up, sir! There are many of us that appreciate the no-nonsense, clinical approach to decision making for our tools. Sincerely appreciate your significant contributions to our art.
Thanks for the feedback. If you guys like it, please share it with like minded readers. 🙂
As always, I write for our fellow patriots and to the advancement of our pool of knowledge.
Excellent write up sir! My name is David Bailey, and I am the COO for Teludyne Tech. If you want to send us that Aero Precision upper we will gladly put our StraightJacket over the barrel you supply! That way you can compare our system to the Christiansen Barrel and any other you want to test against ours. Just give me a call 864-380-0308! You also mentioned barrels that would last a lifetime… Checkout http://www.falkordefense.com they are licensed to manufacture the StraightJacket and they offer a “Lifetime Guarantee” on their ARs ordered with the StraightJacket! We chose Falkor because they use Aerospace Specs to manufacture their ARs, and quite simply our barrels complete this Mazarati of an AR! This article was so thorough so I figured you’d want to know about a truely data driven AR. Thanks!
I cant say no to this offer.
Readers, please stay tuned for a update on The Data Driven AR15 as we evaluate Telludyne Tech’s jacketed barrel and compare it to Criterion’s barrel in a before and after evaluation.
Great article. I’ve learned so much from this site! I love the ‘just the facts and no BS’ style.
Holy crow… I’ve been looking for something -precisely- like this. A numbers and math-driven guide to building an AR-15. Here I thought I was going to have to invest in all adjustable everything that I could lay hands on to get to -my- perfect rifle, but with a pile of relational data at my fingertips, I can take out a load of guesswork, time, and less waste of the almighty dollar, from the development process, and get to it while leaving the guesswork where it should be: personal ergonomics.
I appreciate this article. Too many gun owners are fooled when constructing an AR-15 to buy parts that are sub-par at best. I have a buddy who’s thinking of constructing his own for the first time. I’ll be sure to share this with him.
This is awesome. I don’t get around to reading many blogs and you sent me down a rabbit hole of additional reading. I really really enjoyed the drop in trigger testing and did not even know triggerscan was a thing. Appreciate sharing our barrel testing although it should really be mentioned that these were among barrels that were on the lighter side. One of the big reasons we sat down to get some data out was because of the claims surrounding light weight barrels. In the end I was actually impressed with how well those lightweight barrels shot but do have my questions about how much heat is affecting those profiles. I am continuing to put rounds through some of the barrels to get additional data but the future will hopefully have added profiles notably the ultra lights that people seem to like. I have tried repeatedly to remind people that general purpose AR’s can do things generally well but when we start tweaking in one direction or another like super lightweight or precision oriented the barrel is likely the first thing that needs to change. Your assessment that the criterion is a great barrel seems spot on.
There is so much great info on your site. Actual data rather than some random persons “impressions” of a piece of kit. Thanks for the time and effort and please keep up the good work.
Is there a place to find info/directions on the paracord wrapping done to the Aero handguard?
I will do a wrap post so i can illustrate the wrap. Its quite simple.
Thanks for reading!
Thanks
First off, thank you for your efforts providing the detailed information you posted. Good job.
While I believe MAGPUL is an exceptional company with many, exceptional products, I do not subscribe to drinking ALL of the MAGPUL Kool-Aid. At least I do not in the AR-malite magazine realm. For my money the Allentown, PA manufacturer, LANCER SYSTEMS, has a superlative AR-malite magazine in their L5-AWM series of magazines. Their polymer magazines are a hybrid design with steel feed lips and the body of very indestructive polymer. While the LANCER mags are available in black, OD Green and Flat Dark Earth, they also make them available in a smoke transluscent and a totally clear polymer (of which I am especially enamored of). Ultimately, their steel feed lips are a more assured hedge against feed lip damage vs polymer feed lips (IMO).
Having stated the above, I removed the VLTOR stocks I had on five AR-malite platforms. Their replacement ? MAGPUL’s wonderful, indestructive UBR GEN 1 buttstock ! The UBR with just one feature alone, the fixed cheekrest on an adjustable stock, is unlike ANY other AR-malite platform buttstock. That fixed cheekrest on the UBR is just icing on the cake for a buttstock with numerous features. The UBR is the closest stock one will find to the inherent strength of an actual, fixed buttstock. Evidently, at least to me, those folks evaluating buttstock quality ignored MAGPUL’s UBR GEN 1 (and now GEN 2) stock or just outright dismissed it.
As you and your readers know, all “studies”, “evaluations”, etc., should be taken with a grain of salt. Us readers of such research are seldom privy to the standards utilized in said evaluations. While the MAGPUL and VLTOR products chosen as #1, in their respective categories of AR-malite magazines and buttstocks, are certainly excellent products, my choices are as state above.
Again, thank you for your provided information. It is always good that folks have the opportunity to make choices. I just hope any one person’s choice serves him well in his life and his endeavors.
I agree, there could be any number of products that truly improve on the design of the AR15, but since we dont have data, the article doesn’t feature them.
The lancer is highly regarded, and I would love to see some data driven testing on it, but overall there are many designs that are head and shoulders above the standard USGI mag and if the Lancer is 100% in your rifle then why switch?
Thanks for commenting Dan.
I would like an update to this article come shot show this year in other words after shot show update the article with what new technology comes out
You linked this article in another post, but I found that removing the bearing surface on the opposite lug from the extractor quite interesting, and am now considering taking a file to that lug on my bolts…
“The AR-15 bolt can be thought of as starting with eight lugs around its circumference. One is cut away to provide room for the extractor. During firing, this asymmetry causes the bolt to warp slightly due to uneven support and put approximately 80% of the force load on the two lugs adjacent to the extractor. It’s no surprise that the majority of bolt lug failures occur at one of these two lugs. ArmaLite’s solution is to balance the force by only using six of the seven lugs for load-bearing, restoring symmetry under load. This change is accomplished by simply shortening the back of the lug opposite the extractor so it does not engage the barrel extension. ArmaLite’s engineering study determined that this change alone reduces the stress on the two problem lugs by about 40%.”
http://demigodllc.com/articles/the-armalite-m15a2-infantry-rifle/
Its an interesting idea and if we had another means to test it independently it would seem like an easy fix for bolt life that could be adopted industry wide.
Agree — is it under patent currently? Seems like it must be. BUT fortunately I own a file. Don’t know that it can hurt anything to remove a millimeter or so…
Oh, and would appreciate your thoughts/testing on marking your cam pin with a punch to ensure you always reinstall it with the same side forward.
AND costwise, I don’t see a downside to the PWS camming reciever endplates that can be had for ~$20 at six quantity at botach. QD end plates alone run ~$15 and I have noveske, b5, and bcm currently on rifles… (I don’t regularly use them, but if I want to make my two point sling more of a one point, I move the QD from the rear of my front handguard to below the buffer tube.) My rear attachment point is on my stock on the side opposite my face — it’s not common-sense until after you give it a go. It helps to pull the rifle into your face and it’s proper location towards the center of your chest; whereas on the same side as your face seems to push the rifle away from your face when sling is taut with sling going over trigger hand shoulder and under support hand arm, allowing gun to point muzzle-down if dropping to transition to secondary weapon.
Whats the scuttlebut about marking your cam pin? I haven’t heard of that tip before.
I took a look at the ratchet lock endplate. Looks like a solid idea but I havent tried one. Its been years since I mounted my sling in that position many builds ago.
Lothean,
I cannot imagine the time and effort you had to invest bringing this essay to readers. Simply impressive.
Re: “the best”. Everytime I see a product promoted as “the best” I tend to disregard that rhetoric. “the best” IMO is subjective. What is best for one person is not “the best” for others.
Thank you for your work and effort in bringing forth this information.
“The Best” is merely a popular search term to help guide google traffic. I agree with you that in many cases “the best” can be subjective, but without that label its hard to get readers because the page rank will be so low! 😀 It’s what people search for unfortunately.
I would echo Dan III statements on the comprehensive effort piecing such work in one blog. IMPRESSIVE!! Great research work Lothean and most appreciated by this AR end user!! Kudos and a big thumbs up sir!
Very interesting stuff. As to the lubrications section, I would mention CherryBalmz weapon grease. Yes, grease. Since oils typically use filters, gaskets, pumps and reservoirs, it doesn’t really make sense for guns (since they lack all of those). Mind blown.
regarding rust prevention, I had a need to know and was inspired by the Day At The Range test. I performed a similar test with pieces of sheet metal and repeated salt spray over a week, using various vegetable oils (coconut, avocado, olive) since Frog Lube was rumored to be nothing but a glorified vegetable oil; and BreakFree CLP, USGI LSA, and a thin layer of plain old wheel bearing grease applied with a cloth.
besides the actual vegetable oils being nowhere near the performance of Frog Lube, the Breakfree CLP was a little better than LSA, and the thin layer of wheel bearing grease provided 100% rustproofing.
that leads me to believe that there are no special additives that prevent rust. simply a waterproofing layer that doesn’t evaporate is what does it. the proof was in the pudding. wheel bearing grease blew the rest away and would have been at the top of the list on the Day At The Range testing.
that is an important data point.